The Czech Institute of Informatics, Robotics and Cybernetics at the Czech Technical University in Prague (CIIRC CTU) is entering the fight against COVID-19. CIIRC CTU is developing a respirator prototype under the name “CIIRC RP95” at the RICAIP Centre of Excellence (www.ricaip.eu), funded by the EU. The goal is to develop a respirator that can be produced anywhere in the world on the principle of distributed production, which can off-set a lack of local production capacities or resources. CIIRC CTU encourages industrial and scientific partners, companies, and technically oriented research centres to participate in this endeavour to prepare a prototype respirator for mass production. The aim is to have the respirators printed on 3D printers and be manufactured by injecting plastic into ready-made molds.
Companies and research centres from around the world can apply via email at covid@ciirc.cvut.cz.
All information, including technical requirements, is continuously updated at www.ciirc.cvut.cz/covid.
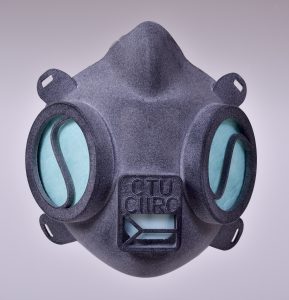
Currently the very effective N95 respirator provides critical protection for doctors and other professionals likely to be exposed to the COVID-19 virus. There is an insufficient number of respirators available on the market, however. The pilot model of CIIRC CTU’s prototype CIIRC RP95 respirator is already being tested. CIIRC CTU chose a completely new 3D printing with MJF technology. The first testing has been very promising, and we are working on minor final improvements and the installation of membrane filters. Upon completion, the respirator will be tested for virus permeability and other critical parameters. Once the CIIRC RP95 prototype is complete, scientists will focus on finding ways to ensure mass production.
The CIIRC CTU initiative is open to research institutions that have two core technologies: an HP Multijet Fusion 4200 printer to print the respirator skeleton in plastic, and the Stratasys Polyjet J750 to print the longer lasting rubber or silicone exhalation valve. Other 3D printing technologies must always be assessed individually for the air-tightness of the manufactured part and also with regard to health safety. Once prepared, the respirator will be assembled with the filter element. The CIIRC RP95 can be used repeatedly, of course, and the filter material can be replaced. The inlet opening for the filter element can be adjusted to any shape according to the suppliers‘ specifications.
Since the required equipment is not common, the CIIRC CTU team is also examining a mass production model that will utilize a material injection mold, also printable on 3D devices. CIIRC CTU is looking for partners, especially manufacturing companies with experience in the injection-molding process, to develop the requirements needed to design the shape of the injection mold.
Once the prototype has been tested, CIIRC CTU will share the technical specifications among partners in Europe and worldwide. It will be the first distributed production during the COVID-19 emergency. This is also the key model of cooperation targeted by the RICAIP Research Centre.