Thank you for your interest in the details of our demo stations!
We are currently preparing a comprehensive overview of all the activities we’re planning – and some of them are already available to explore on this page. Information about each station, the topics they cover, and the people you’ll meet there is being added gradually, so keep checking back to make sure you don’t miss anything.
We recommend going through the list of available demo stations below and discovering what interests you most. We look forward to seeing you!
Robotic 3D Printing from Polymers and Metals
Focus: Additive manufacturing, 3D printing
Lead: Tomáš Jochman
Location: RICAIP Testbed Prague, Ground Floor, Building B
Robotic 3D printing opens new possibilities in additive manufacturing, both for production and repair of existing parts. Thanks to the robot’s large working area, it is possible to work with parts that cannot be made using traditional 3D printers. We will also showcase robotic 3D printing with a Meltio laser deposition head, which allows printing with two metal materials simultaneously. Additionally, we’ll present our research results enabling the design of robotic 3D printing workflows using a digital twin, optimizing the entire process.
3D Reconstruction and Robotic Manipulation in Manufacturing incl. 3D Gripper
Focus: Flexible Manufacturing
Lead: Martin Mikšík, Artem Moroz
Location: RICAIP Testbed Prague, Ground Floor, Building B
Our in-house robotic arm precisely scans an object and creates an accurate digital 3D model. Thanks to a special calibration method, we achieve very high scanning accuracy. The generated 3D model is then used by other robots for tasks such as picking objects from a bin (so-called bin picking). A key technology here is the 6D pose estimation method developed at CIIRC CTU. The six degrees of freedom (6D) describe the full position and orientation of an object in space, including three coordinates for location (x, y, z) and three angles for rotation. A robot equipped with a camera uses this advanced AI-based method to compare the camera image with the digital 3D model in real time, enabling it to accurately grasp the target part. This system is further enhanced with advanced technology for automatically generating a 3D model of a specific tool — a suction gripper. Based on a precise CAD model of the manipulated object and user-defined grasp points, our software can automatically design and generate an optimized 3D model of the suction gripper. The combination of these technologies enables the automation of complex manipulation tasks that were previously difficult or hazardous for human operators and contributes to the development of flexible and safe robotic manufacturing within the Industry 4.0 framework.
Digital Twin and NVIDIA Omniverse
Focus: Digital twin, process simulation, AI model training
Who it helped: Continental Automotive Czech Republic
Lead: Tomáš Jochman
Location: RICAIP Testbed Prague, Ground Floor, Building B
The NVIDIA Omniverse project brings new opportunities for industrial digital twins. It allows for precise simulation of production processes, robot path verification, and real-time error detection. Its realistic visual environment and random scene generation support efficient AI training for object recognition and 6D pose estimation. We’ll show how this can be integrated into a digital twin for safe testing and more effective collaboration. Our research shows how Omniverse helps bridge the gap between simulation and reality, optimizing complex industrial applications.
Production Optimization Using the Example of a Galvanizing Line (Data Collection and Analysis)
Focus: Production analysis based on data collection, optimization
Who it has helped: LAKUM-GALMA
Lead: Pavel Hradecký, Václav Kubáček
Location: RICAIP Testbed Prague, Ground Floor, Building B
Using the example of intelligent control of a galvanizing line, we demonstrate how we link data from ERP orders with real-time production processes (SCADA → PLC → MES) and deploy algorithms for automatic scheduling and planning. This ensures balanced utilization of line resources and improved production throughput. We digitize recipes, collect and analyze production data, implement automated decision support, and provide clear dashboards for management. This reduces lead times, minimizes reliance on expert manual interventions, and paves the way for data-driven surface treatment of metals. Come see how we can help bring your production into the Industry 4.0 era.
WAAM and HM Technologies
Focus: Additive manufacturing and 3D printing
Who it has helped: Developed in cooperation between RCMT CTU and engineering firm Kovosvit MAS. Particularly advantageous for complex-shaped parts where significant material removal would be required, such as ship propellers, Pelton turbines, mold parts, etc.
Lead: Ing. Tomáš Fornůsek, Ing. Ivan Diviš
Location: RICAIP Testbed Prague, Basement, Building B
This metal 3D printing technology, fully developed in the Czech Republic, belongs to the category of Hybrid Manufacturing. It allows for the creation of metal parts through arc welding and machining within the same workspace at significantly lower costs. The WeldPrint 5AX machine enables the creation of metal components using arc welding and their machining in a single setup. Ongoing research and development now focus mainly on processing stainless steels, tool steels, and Inconel alloys. The developed technology can be used not only by top-tier R&D centers but also profitably by regular small and medium-sized engineering firms.
Machining Technologies and Digital Twins
Focus: Technology
Who it has helped: Improved productivity and error elimination during the implementation of advanced machining technologies for companies like TOS Varnsdorf, BRAY, TOS Kuřim – OS, Kovosvit MAS, ŠMT, TAJMAC-ZPS, TGS Tools-Machines-Technological Services, CNC Tvar, and others.
Lead: Ing. Michal Stejskal, Ph.D., Ing. Petr Mašek, Ph.D.
Location: RICAIP Testbed Prague, Basement, Building B
Machining process digital twins offer many advantages – they detect errors before they occur on the machine, help optimize production processes, save costs, speed up production, and reliably predict machining outcomes. They also support companies in aligning their production with sustainability goals. Digital twins significantly contribute to improved reliability, shorter lead times, and production preparation. They are successfully used for predictive control and optimization of NC machining strategies during process design, optimizing process parameters and machine settings to achieve higher productivity and better quality and accuracy. They are suitable for both one-off and mass production in sectors like energy, aerospace (thin-walled parts), and mold manufacturing. Process digital twins also support real-time monitoring of actual machine operations by reading high-speed data (500 Hz) from the machine, allowing real-time simulation of machining and tool wear detection. Their versatility makes them uniquely applicable to various machining processes and enables significant cost savings through better tool usage. These twins are a key enabler for digitizing processes and implementing autonomous manufacturing systems.
Laser Technologies – USP, LMD
Focus: Technology
Who it has helped: Rotana, Dormer Pramet, PBS, European Cryogenics, Lintech, LaserTherm
Lead: Ing. Adam Čermák, Ph.D., Ing. Martin Novák
Location: RICAIP Testbed Prague, Basement, Building B
The testbed is equipped with advanced Ultra-Short Pulse (USP) laser machining technology, enabling precise processing of various materials, including ultra-hard and brittle ones. The system features a femtosecond laser with three selectable wavelengths (1030 to 343 nm), a repetition rate of 0.2 – 1 MHz, integrated with a high-dynamic galvo-scanning system and controlled via an open control interface. This technology enables extremely precise micromachining and surface texturing at micro- and nano-levels with high reproducibility. The ultra-short pulse interaction time minimizes thermal effects, which is key for delicate materials or when producing functional textures with high precision. The setup is also suitable for selective ablation (laser stripping), micro-drilling, and other applications in fields such as medicine, electronics, and microfluidics.
Additionally, the testbed houses robotic additive manufacturing technologies, including a laser robotic cell equipped with two interchangeable heads for Laser Metal Deposition (LMD), used to build metal parts from powder or wire using a laser. Operated by a KUKA industrial robot and Sinumerik system, the cell can manufacture complex parts or repair damaged ones, such as tool components. Compared to arc welding, laser technology introduces less heat into the part, resulting in lower residual stresses and reduced deformation. A key research topic is in-process thermal field monitoring to prevent overheating and resulting geometric defects. Laser power optimization across layer groups significantly enhances final part accuracy and surface quality.
Large-Format Robotic 3D Printing – PEM
Focus: Additive manufacturing and 3D printing
Who it has helped: Compotech, Bluetech, eForce Prague Formula, TGS Tools-Machines-Technological Services
Lead: Ing. Michal Rytíř
Location: RICAIP Testbed Prague, Basement, Building B
Pellet Extrusion Modelling (PEM) is a large-format robotic 3D printing technology using thermoplastics. The extruder head, mounted on a robot, enables the printing of components in various shapes and structures. Unlike desktop 3D printers, PEM offers high productivity by using plastic pellets instead of filament and leverages the robot’s full reach for a large working area. It can produce any shape as long as 3D model data is available. Applications include:
- Composite molds – engineering
- Furniture and urban furnishings – design
- Vacuum jigs – aerospace
- Models – architecture
- Rapid prototyping – engineering
Research focuses on process monitoring and feedback-controlled print speed to achieve homogeneous parts with good layer bonding and mechanical properties. This also involves developing NC code and path control for the robot.
Robotics and Automation
Focus: Robotics
Who it has helped: Robotic assembly of optical elements, bin picking of metal stampings, automation in food processing…
Lead: Ing. Jaroslav Seifrt, Ing. Štěpán Fiala, Ph.D.
Location: RICAIP Testbed Prague, Basement, Building B
In the robotics and automation domain, the Testbed offers proof-of-concept solutions and complex automation task implementations. Together with customers, current workplaces are analyzed to identify automation and robotics opportunities for partial or full production lines. Unique elements of proposed solutions, customized to specific workplaces, are physically tested in our labs equipped with robotic cells from various manufacturers – Fanuc, KUKA, ABB, Staubli, and others. Specific components (grippers, end effectors, jigs) and processes (vision systems, high-precision handling) are tested. 3D printing and rapid prototyping principles are used for testing. These tests feed into accurate simulations of entire systems using tools like Visual Components, enabling time and space analysis, production flow visualization, control logic preparation, and more. Thanks to experience with various systems, our designs are brand-agnostic and focused on effectiveness.
Machine Operation Support
Focus: Machine operation
Who it has helped: Machine tool manufacturers and users, e.g., TOS Varnsdorf, TOSHULIN, TOS Kuřim – OS, Kovosvit MAS, TAJMAC-ZPS, SAHOS, TGS Tools-Machines-Technological Services, TOS Hostivař, Slovácké strojírny – plant 08 TOS Čelákovice, TRENS SK, DN Solutions Co
Lead: Ing. Jan Moravec, Ph.D., Ing. Eduard Stach, Ph.D., Assoc. Prof. Ing. Martin Mareš, Ph.D.
Location: RICAIP Testbed Prague, Basement, Building B
Machine operation support includes key technologies and methods to ensure the high precision and reliability of machine tool operations. These involve drive tuning for dynamic behavior optimization (impacting surface finish and production efficiency), methods for geometric error measurement and compensation, and software-based thermal compensation to reduce the impact of temperature-related deformations on precision. Demonstrations include advanced diagnostics and practical methods to improve accuracy and performance under real operating conditions.
Machine and Assembly Group Development Including Simulation Support
Focus: Machine development
Who it has helped: Optimizing the design of machine tools for many Czech manufacturers such as TOS Varnsdorf, TOSHULIN, TOS Kuřim – OS, Kovosvit MAS, TAJMAC-ZPS, Slovácké strojírny – plant 08 TOS Čelákovice, Erwin Junker Grinding Technology, Strojírna TYC, SAHOS, TOS Hostivař, and others
Lead: Ing. Jaroslav Červenka, Ing. Matěj Sulitka, Ph.D.
Location: RICAIP Testbed Prague, Basement, Building B
The development of machines, functional units, and components must meet customer requirements for functionality, operational characteristics, production productivity, and, last but not least, cost. The shortening of development cycles and tight delivery deadlines put pressure on minimizing development time. These goals can be achieved through the support of advanced simulation tools and digital twins, which make it possible to verify the proposed properties and operational behavior of machines and assemblies in a virtual environment and using virtual prototypes, in relation to their intended technological application. This approach allows for the elimination of errors that would otherwise require the production and testing of physical prototypes. As a result, it is possible to significantly reduce costs and shorten development time. The presentation will showcase examples of machine development and virtual testing of machines, milling heads, spindles, as well as original procedures aimed at minimizing geometric errors of machines. During development, advanced optimization techniques are applied, such as topological and parametric optimization, thermal behavior simulations, and integrated models of drive interaction and drive control with the supporting structure. These models enable the successful design of systems with balanced control parameters and mechanical structure characteristics.
Voice and Gesture Control of Robots and Risk Awareness in Robotic Manipulation
Focus: Collaborative Robotics
Who it helped: Robotwin, Factorio Solutions, Bosch Research
Lead: Karla Štěpánová
Location: A404 (live demo)
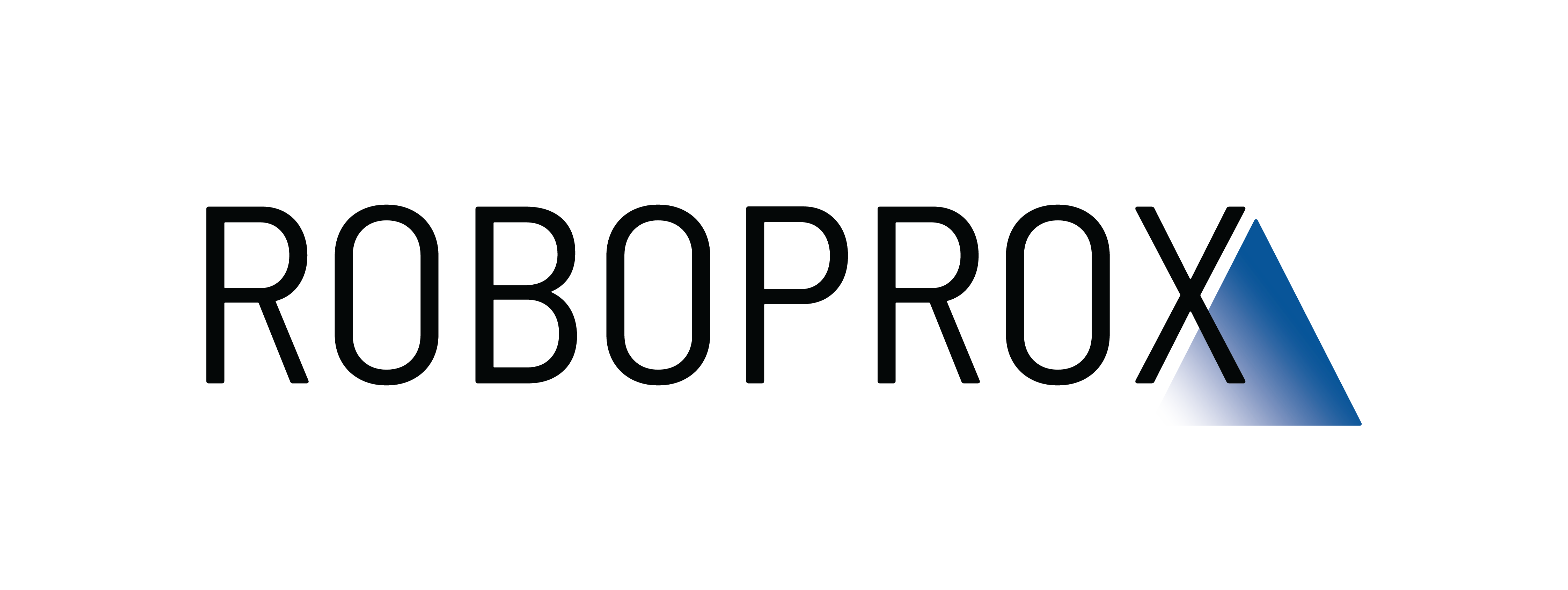
Controlling a robot using voice commands, gestures, and demonstrations enables simple and intuitive reprogramming of robots in new situations, as well as a natural way to explain task- or environment-specific conditions to the robot. To ensure that kinesthetically taught trajectories can be executed safely in a new environment, we have developed a safety execution module that allows the robot to stop in the event of an unexpected situation.
Process Optimization in Manufacturing, Healthcare, Logistics, Energy, Defense, and More
Focus: Process optimization, AI in industry, data-driven methods
Who it helped: Škoda AUTO, PPL, ERA, EATON, Continental, Beckman Coulter, Siemens Energy, DECCI, Air Navigation Services CR, MÚÚÚ Písek, Blumenbecker, FN Hradec Králové, FN Motol, FN Královské Vinohrady, Purem Rakovník, Znojmo Hospital, Humanomed, Pointee
Lead: Přemysl Šůcha
Location: RICAIP Testbed Prague, Ground Floor, Building B
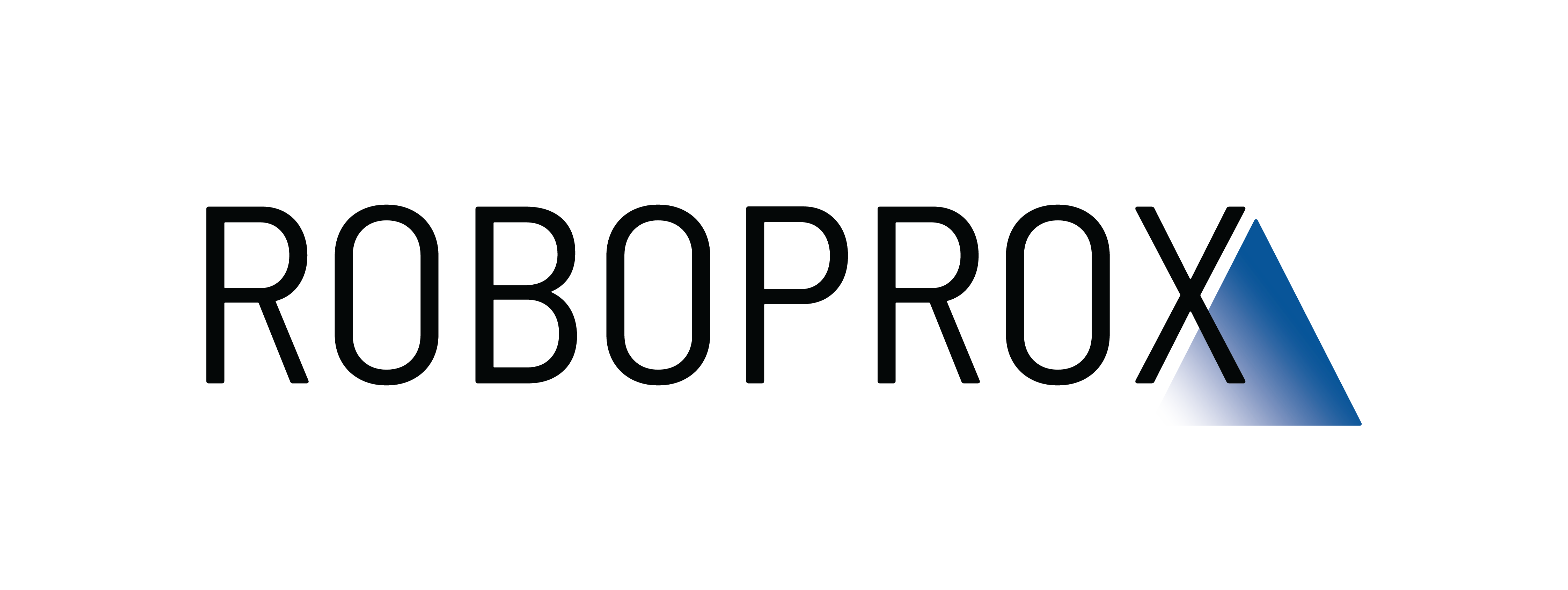
Our group focuses on analyzing, simulating, and primarily optimizing any kind of process. We base our optimization methods on mathematical principles, extending them with data-driven and AI techniques to fit specific operational needs. We have over 20 years of experience in this field.
Autonomous Vehicles
Focus: Autonomous vehicles, AI driving, real-time software
Who it helped: Porsche Engineering, Škoda Auto, Digiteq Automotive, TÜV SÜD
Lead: Michal Sojka
Location: JP-A122 (Autonomous Vehicles Lab)
We work on autonomous vehicles across the entire stack – from electronics and low-level (real-time, safety) software to AI-based driving applications. Our experiments start in simulators and are always validated on real vehicles. We have implemented projects for automated parking, Automated Lane Keeping Systems (ALKS), and are currently working on intersection navigation.
Intelligent Decision-Making and Planning
Focus: Automated planning, intelligent decision-making
Lead: Lukáš Chrpa
Location: RICAIP Testbed Prague, Ground Floor, Building B
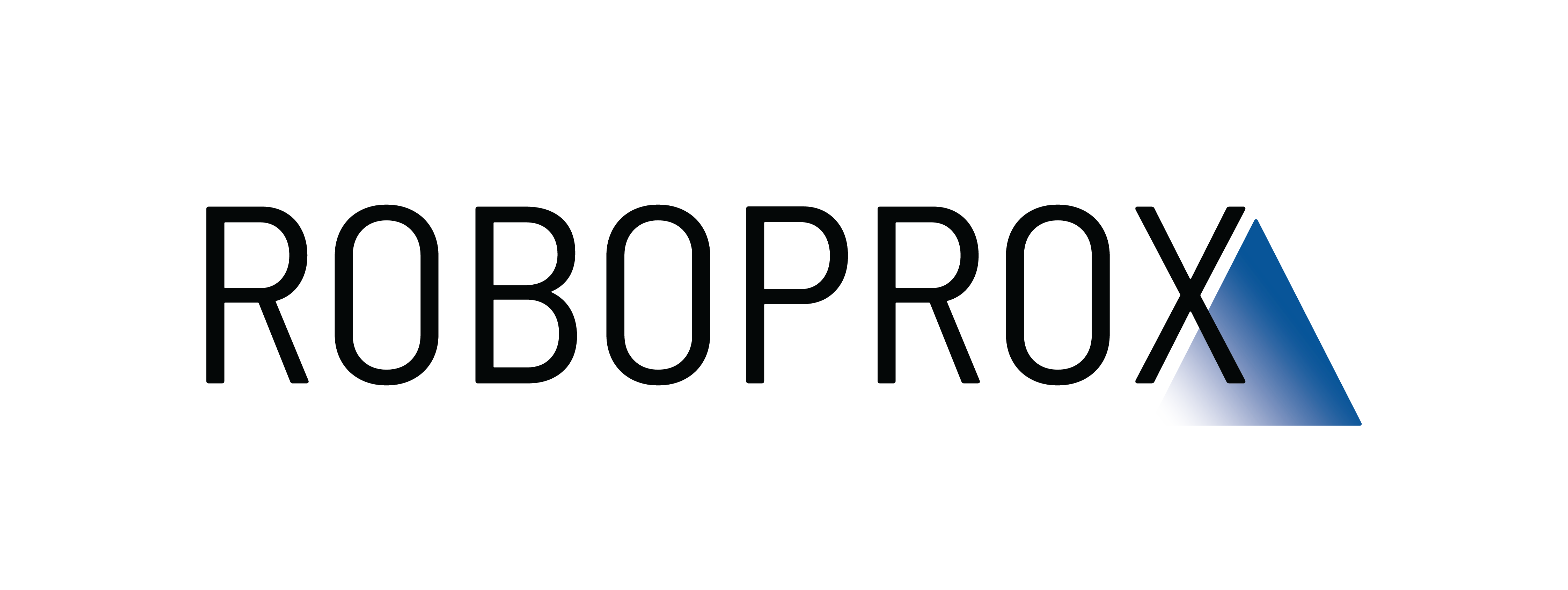
We research techniques for automated planning and intelligent decision-making. Our focus includes centralized traffic routing and the concept of “planning against nature,” which allows autonomous entities to make deliberative decisions in dynamic environments influenced by natural phenomena or other agents.
Visual Navigation of Mobile Platforms in Infrastructure-Free Environments
Focus: Visual navigation, autonomous mobile platforms, flexible manufacturing systems
Who it helped: Třinecké železárny a.s., HOPAX a.s., Military Repair Enterprise (VOP)
Leads: Libor Přeučil/Tomáš Pivoňka, Viktor Kozák
Location: B320 (Intelligent and Mobile Robotics Lab)
We develop principles and procedures for fully autonomous visual navigation of mobile platforms (e.g., manipulators, logistics robots, vehicles) in complex and dynamic environments. Applicable for both UGVs and UAVs, indoors or outdoors, and even under uncertainty. Alternative approaches use LIDAR-based methods. Our solution can be added as a cost-effective unit to any drive-by-wire mobile system – ideal for highly flexible production systems, automated warehouses, and surveillance tasks.
Planning and Scheduling for Robotics, Especially in Logistics
Focus: Robotic process optimization, logistics algorithms, warehouse management
Who it helped: GrenzeBach GmBH, SwissLog AG, Wienerberger A.G., ATG s.r.o, TFE France
Leads: Libor Přeučil/Miroslav Kulich, David Zahrádka
Location: B320 (Intelligent and Mobile Robotics Lab)
We develop advanced optimization algorithms that significantly improve process productivity. Our research and development focus mainly on NP-complete problems like Fetch and Carry, Anytime planning, and distribution network optimization, with applications in warehouse and fleet management.
Advanced Robotic Manipulation: Inspection Tasks, Pick & Place
Focus: Robotic manipulation, optical guidance, machine vision
Who it helped: Škoda Auto (2x), ATG s.r.o., LEGO (2x)
Leads: Libor Přeučil/Lukáš Bertl, Viktor Kozák
Location: B320 (Intelligent and Mobile Robotics Lab)
We address tasks involving inspection and/or grasping of parts whose 3D position is not precisely known or difficult to determine with standard methods. Solutions include target-oriented optical guidance of manipulators to randomly placed parts, with optimal sequencing of such operations. We also develop robust machine vision methods for industrial applications, even in challenging conditions, using monocular RGB(D) cameras.
Process Monitoring and Optimization
Focus: Predictive Process Maintenance, Manufacturing Data Analytics
Who it helped: Prague City Hall – Department of Environmental Protection (data cleaning from waste container fill-level sensors and optimization of waste collection), ŠKODA AUTO (dimensional quality control of machined engine heads)
Leads: Martin Macaš
Location: RICAIP Testbed Prague, Ground Floor, Building B
Modern multidimensional process monitoring enables the use of machine learning in the form of anomaly detection or standard multi-class classification. The first step is to train detectors using historical data to recognize inefficient, incorrect, or non-standard processes. The detected issue can then be diagnosed, explained, and resolved to optimize the overall process. This approach is demonstrated using examples such as the monitoring and optimization of a robotic assembly process or the process of depositing waste into large-capacity containers.
Optimization of Factory Layouts
Focus: Production optimization, spatial layout, AI in industry
Who it helped: Škoda Auto, Continental, ZŤS VaV, DEL
Lead: Petr Kadera
Location: RICAIP Testbed Prague, Ground Floor, Building B
Efficient factory operation depends heavily on spatial layout, which becomes more complex with growing process sophistication. AI methods help solve problems with many often conflicting criteria, such as fitting in as many production lines as possible, minimizing logistic paths, and avoiding co-locating incompatible technologies.
Control of Flexible Factories
Focus: Flexible manufacturing, production control, small-batch automation
Who it helped: Rockwell Automation, CertiCon, LEGO, ZŤS VaV, DEL
Lead: Petr Novák
Location: RICAIP Testbed Prague, Ground Floor, Building B
Many industries are experiencing a growing number of product variants, which lowers the effectiveness of automation originally designed for mass production. Model-driven production control enables responsiveness to changing demands and efficient production of small batches.
Supporting Efficient Programming of Robotic Welding Cells
Focus: Robotic welding, automation of programming, CAD/CAM integration
Who it helped: ALAD CZ s.r.o., STP-Plast s.r.o.
Lead: Vladimír Smutný
Location: RICAIP Testbed Prague, Ground Floor, Building B
One key obstacle to deploying robotic welding cells in low-volume production is the high cost of manual programming. Replacing expert human effort with automated programming processes eliminates this barrier, enabling small- or single-series production. In our approach, robot trajectories with 9–11 degrees of freedom are automatically generated in confined spaces defined by the product’s shape. Inputs include CAD geometry and CAM-generated weld positions and shapes.